A group of team members and I collaborated to brainstorm, test, and develop an ultralight (UL) backpack for women seeking to travel lighter and faster during long-distance backpacking trips.
This project was a pivotal experience in my development as a leader and innovator. It honed my ability to manage complex, interdisciplinary tasks, from guiding a team through multiple prototyping stages to integrating stakeholder feedback under tight deadlines. I grew in my capacity to foster effective communication, allocate responsibilities, and keep a project on track despite challenges. Most importantly, I gained hands-on experience in the full life cycle of a product—from concept to physical product and even end-of-life considerations. The positive reception of our final product validated our efforts and reinforced my passion for creating solutions that are both functional and environmentally conscious.
Within this project, I helped lead product development and design with another individual in addition to owning the sustainability category, guiding group goals/focus and timeline.
The project process first began with a consumer survey of 40 individuals, providing insight into common issues with traditional backpacks (i.e. shoulder pain, difficulty accessing items, fatigue, and upper back pain). This market research illuminated the opportunity to target a durable, ultralight-style backpack for women at a lower price range.
As a result, materials for the backpack were selected for their durability and raw material cost, with lower regard for weight. Two prototypes (one muslin, one with nylon) were created before sewing the final pack. Key features include a roll top closure, elastic front and side pockets, padded straps, hip belt pockets, and an external bear can holder.
First Prototype
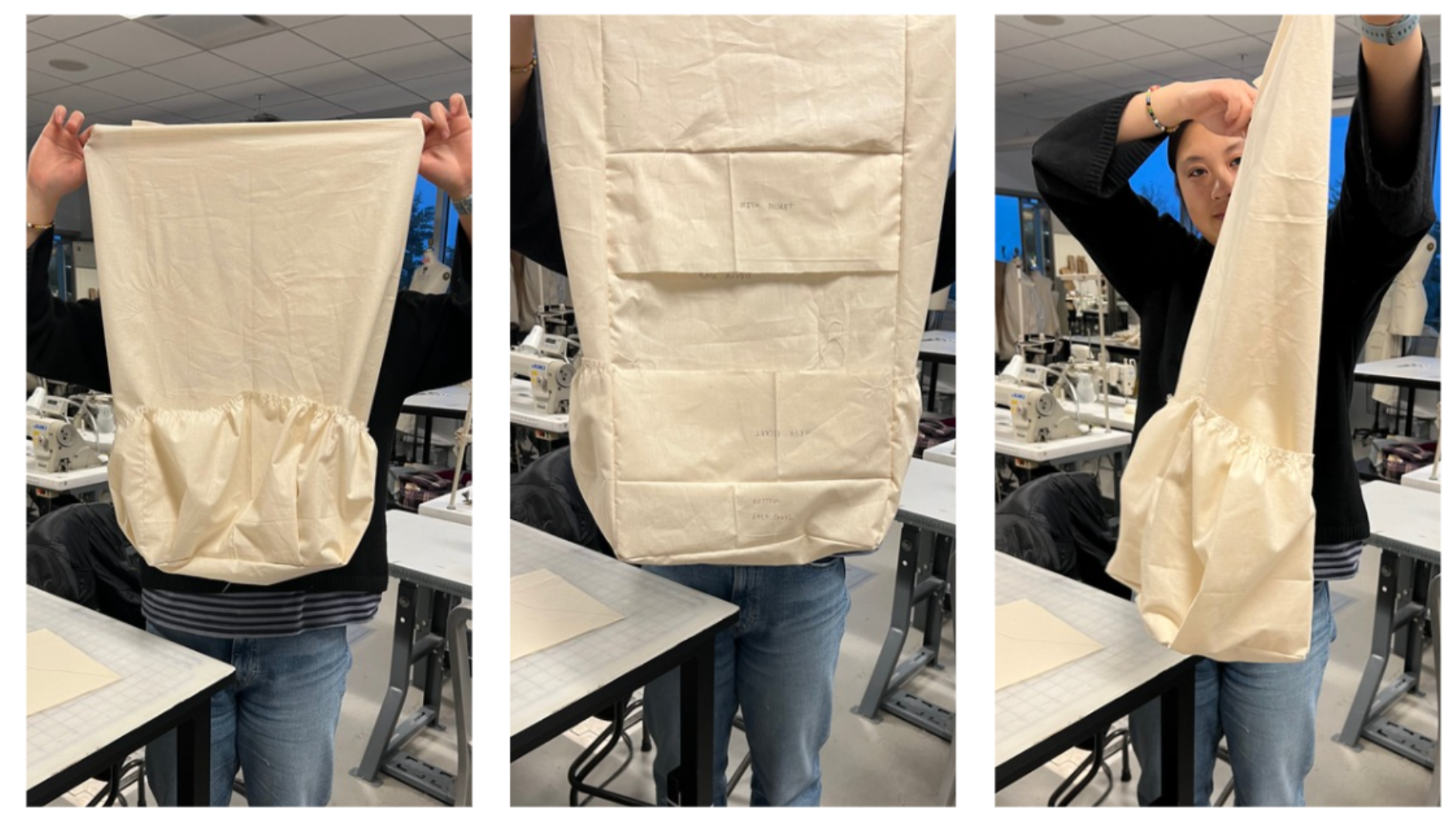
Our first prototype was made from muslin to test the dimensions of the bag and the mechanics of the water bottle pocket (Figure 5). We liked the size of the bag so proceeded with our second prototype using more technical fabrics.
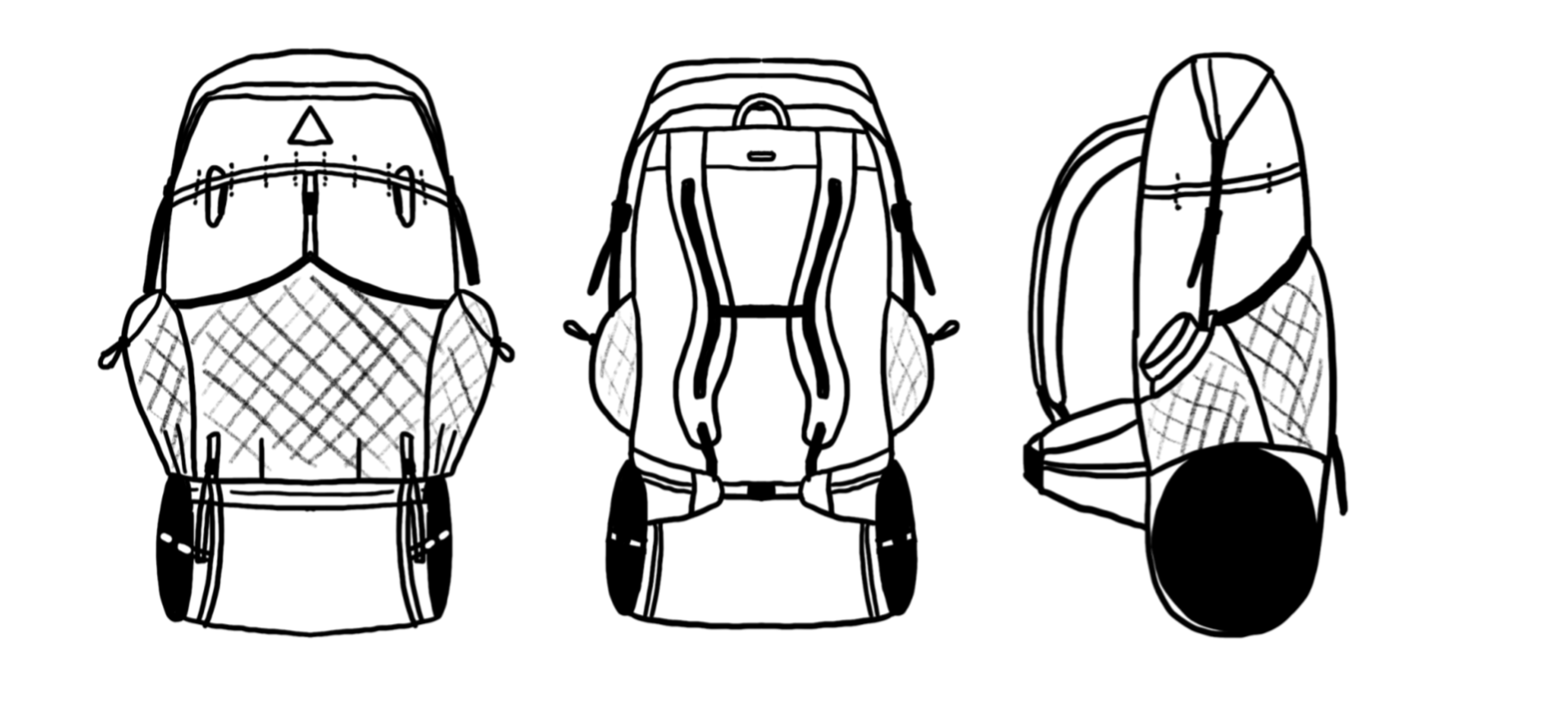
First sketch of our pack. Notable features are the roll-top closure, front mesh pocket, angled side pockets, S-shaped straps, hang loops, hip belt with pockets, and external bear can holder.
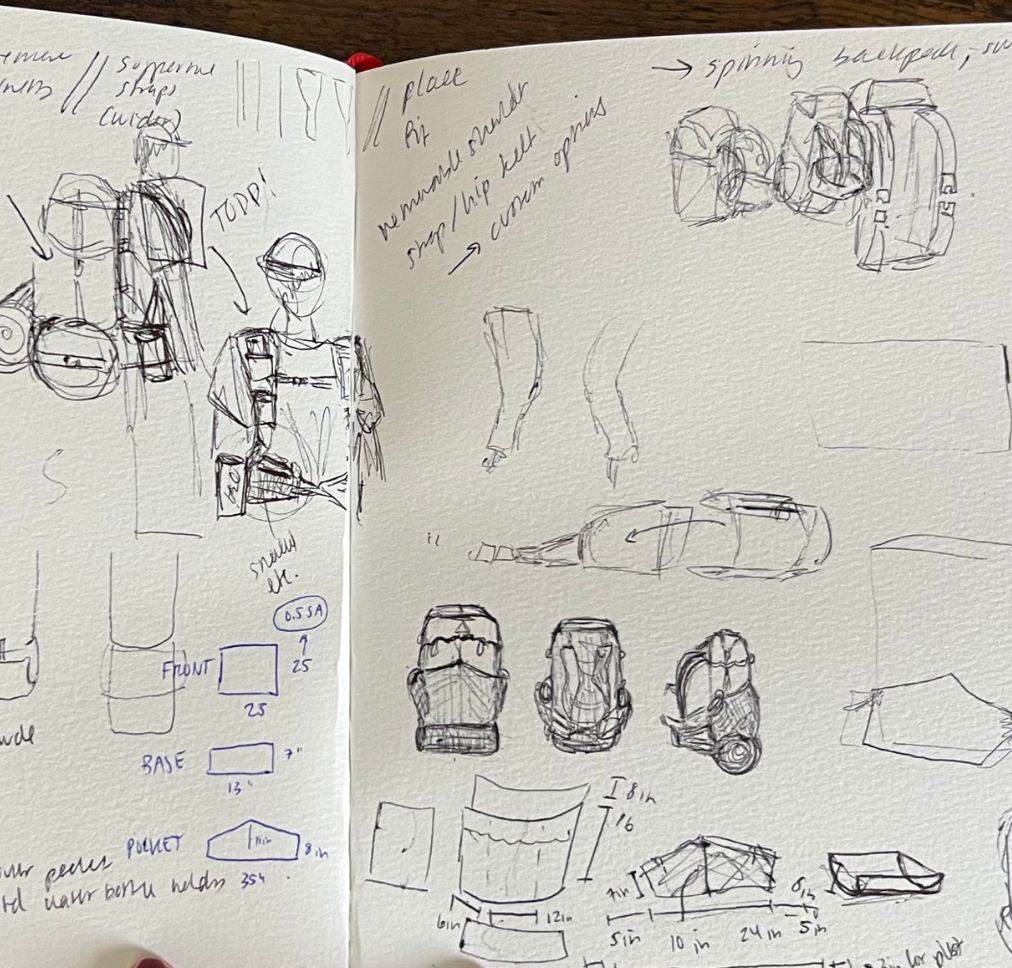
Second Prototype
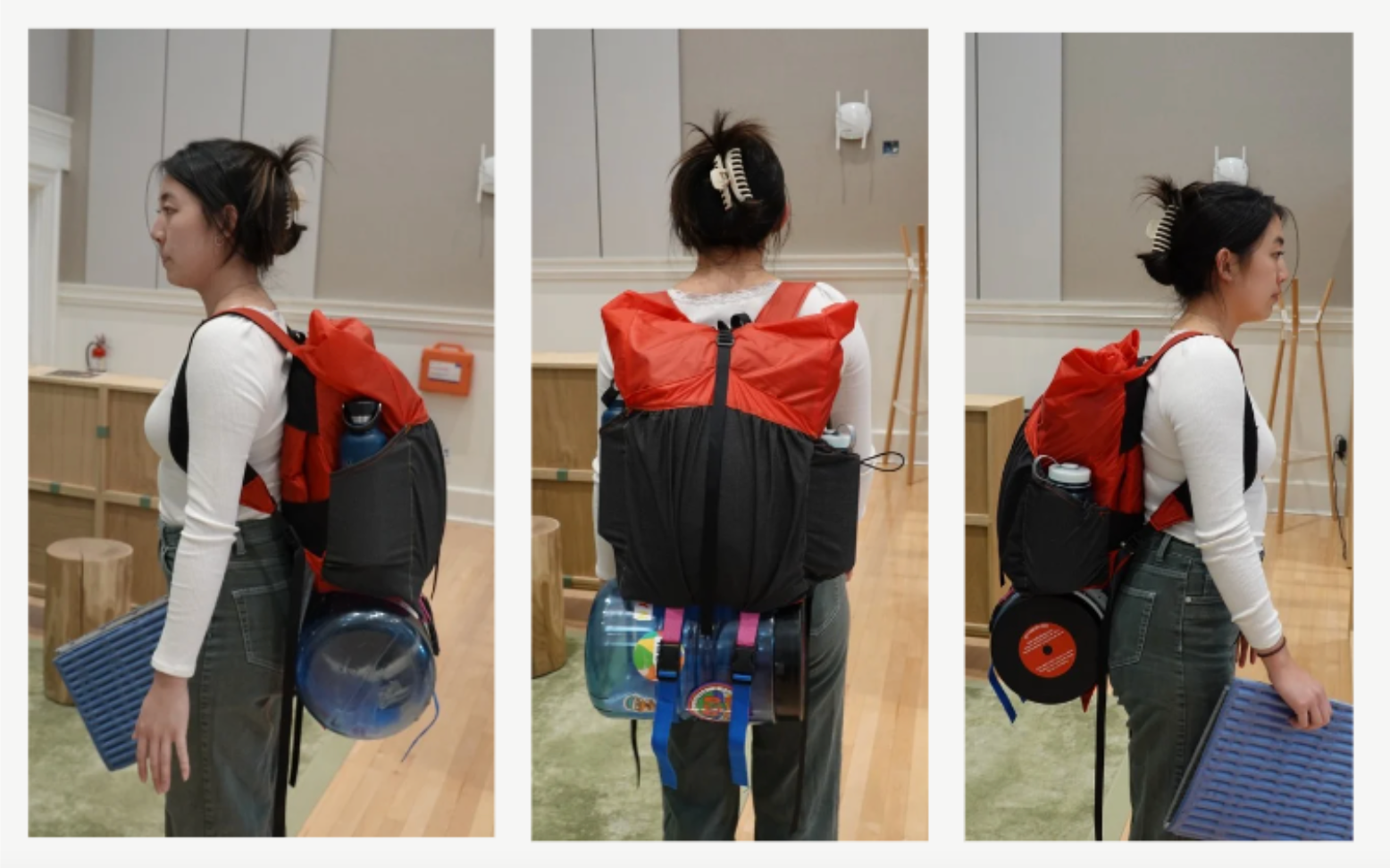
The second prototype was created using 1.9 oz nylon ripstop, Venom UL stretch mesh, and ¼" 3D spacer mesh, as well as scavenged hardware and webbing. The dimensions, front pocket, and water bottle pockets were to our liking, but there were areas for improvement. The straps were flimsy and not very supportive, the roll-top closure was difficult to contain with only one strap to secure it, and the back pad slipped out of its pocket easily. The red nylon ripstop felt cheap and attracted dirt. The bear can holder flap could be extended and a thinner webbing could be used.
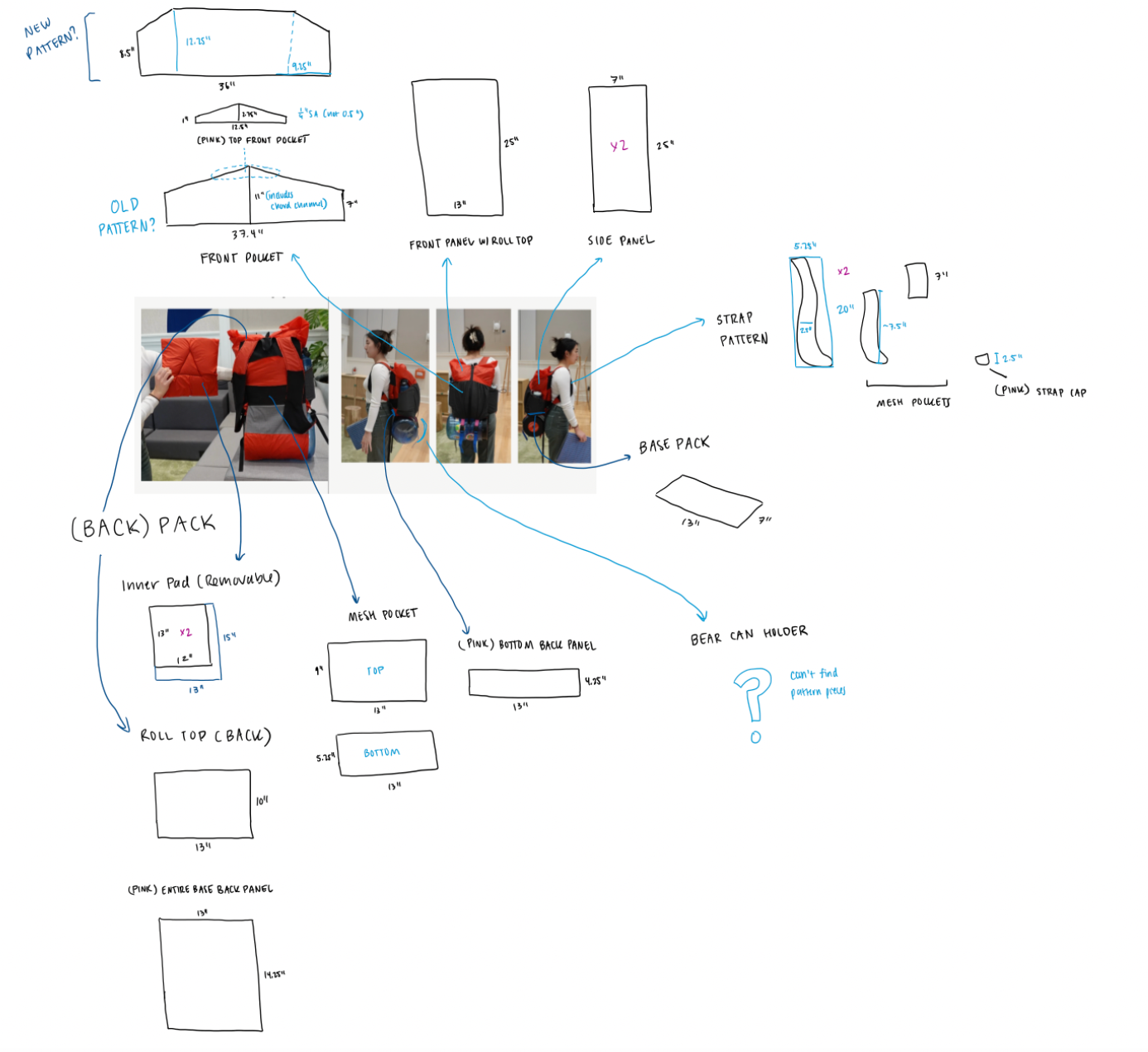
Pattern Planning for Second Prototype
Final Backpack
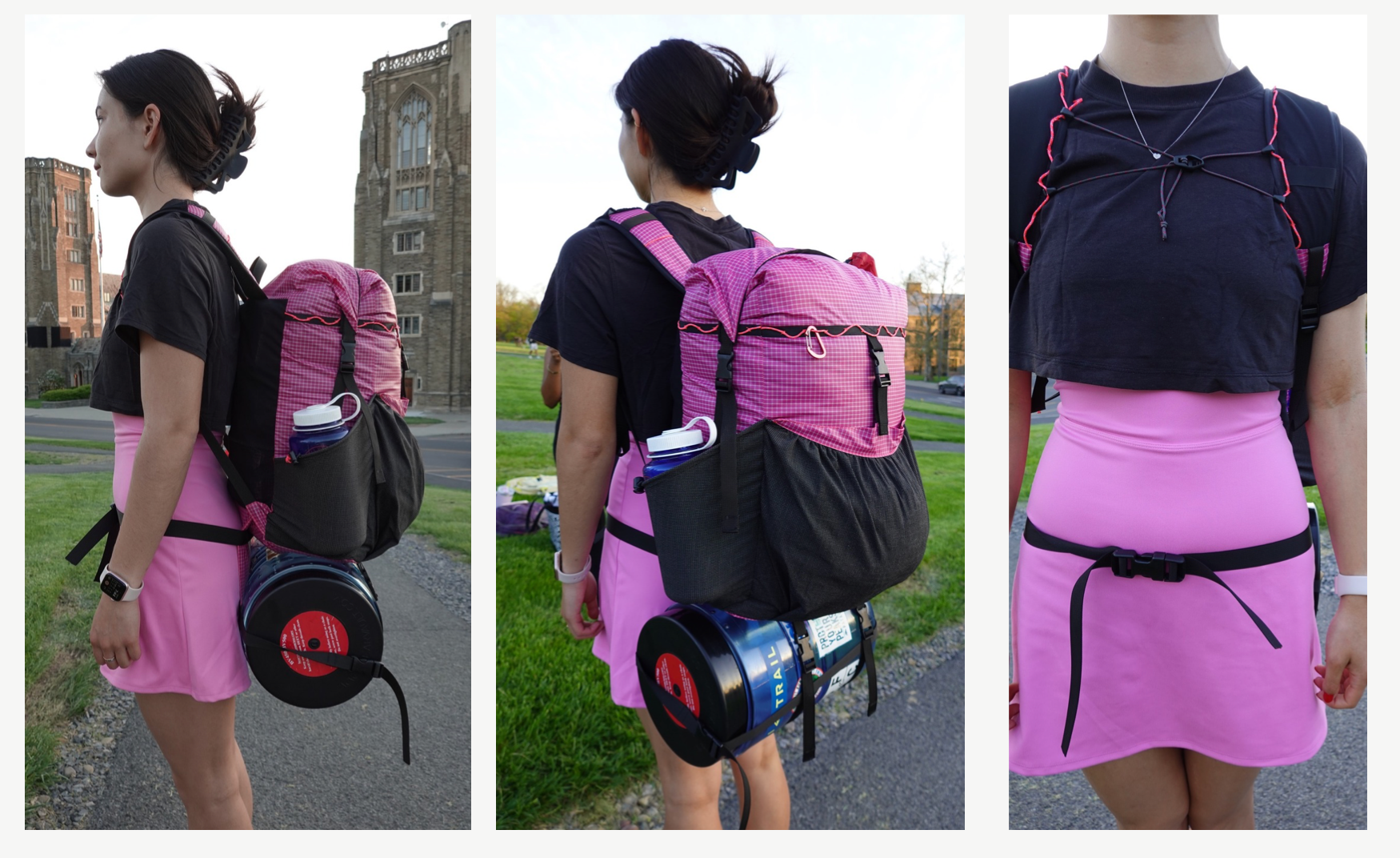
The final backpack improved greatly upon the second prototype. First, the 1.9oz nylon ripstop was replaced with 210D nylon reinforced with a Dyneema grid structure. The new fabric weighed 3.9oz/yd2, but was much more durable, tear-resistant, and came in pink. After receiving feedback at a stakeholder meeting, we doubled up on ¼" spacer mesh padding on the straps. They turned out much more comfortable and sturdy than our first attempt. The roll-top closure was improved by securing it on the two side panels of the pack. Hang loops and webbing were added to the pack and the straps. The front and side pocket design remained the same, but the bear can holder was extended. A removable hip belt, and hip belt pockets, were also added to the final pack.
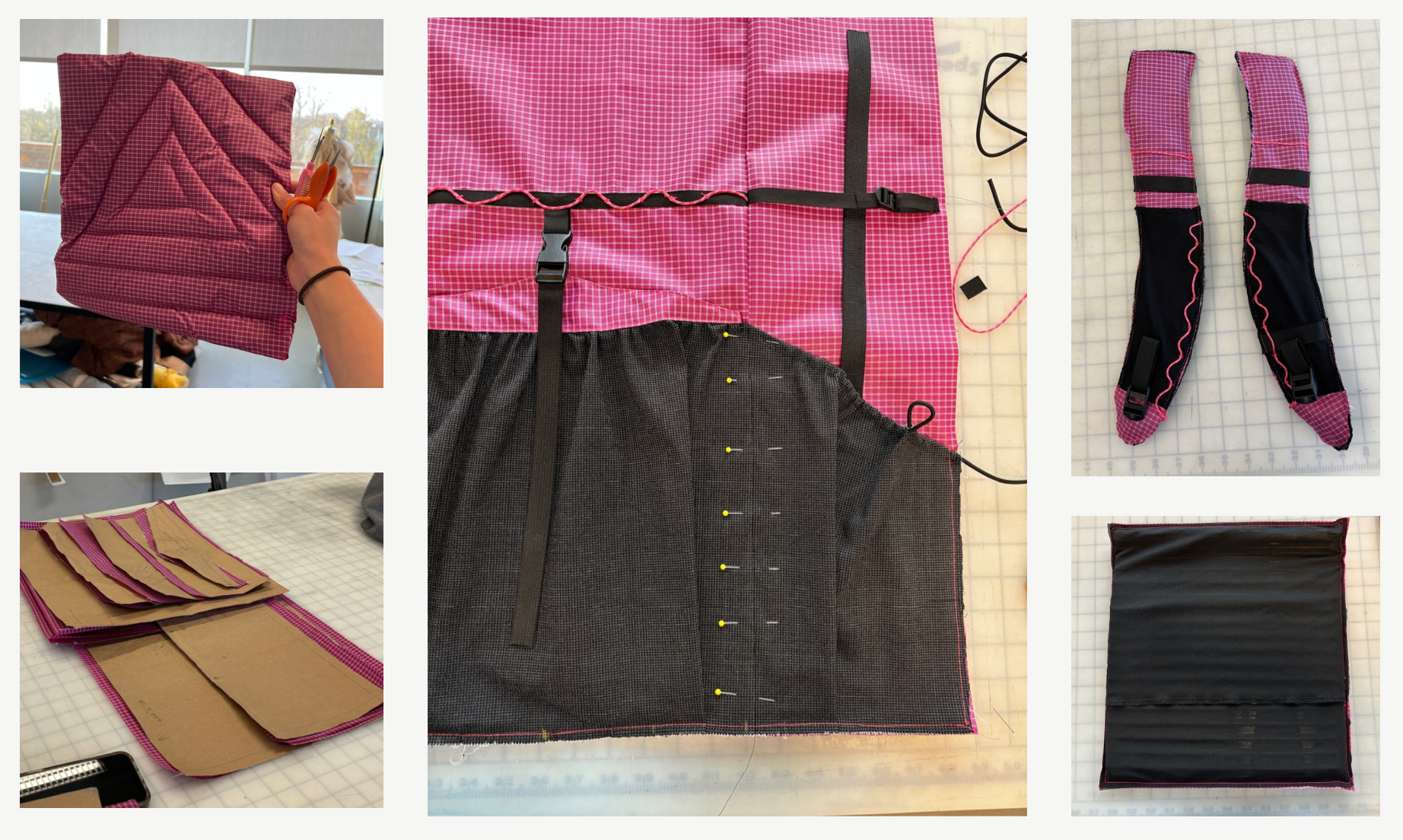
Sustainability
In product development, we prioritized sustainability from design to disposal. The packs are engineered for disassembly, using limited types of fabrics and fewer seams, while avoiding glue altogether, to simplify recycling processes. The simple four-panel and bottom construction allows for easy seam access and unpicking if it is necessary to replace or reinforce a section. While the pink outer fabric contains a PFC-free durable water-repellent (DWR) finish, the inner seams were not taped. This allows for easier repair and fewer materials used. The pack could be considered water resistant, but not waterproof. However, an easy fix is to line the pack with a reusable plastic bag.
We've also implemented innovative ways to reuse fabric offcuts by turning them into cushioning and padding for the packs, reducing waste. In terms of future customer relations, we plan to gain engagement in our sustainability efforts through educational initiatives in addition to offering both DIY repair options and a professional take-back program. These initiatives ensure that the packs can be easily mended and repurposed, extending their lifecycle and lessening their environmental impact.
Group Members and Roles
Ashley Liaw - Owner, Product Development/Design, Sustainability
Mikayla Lin - Owner, Design & Product Development
Katrina Reichenbach - Owner, Performance Testing
Christina Simon - Owner, Materials Testing
Astrid Day - Owner, Marketing
Riya Yerramilli - Owner, Business Management
Leah Rosenkranz - Owner, Supply Chain