Knitted Strain Sensor Material and Structural Enhancement
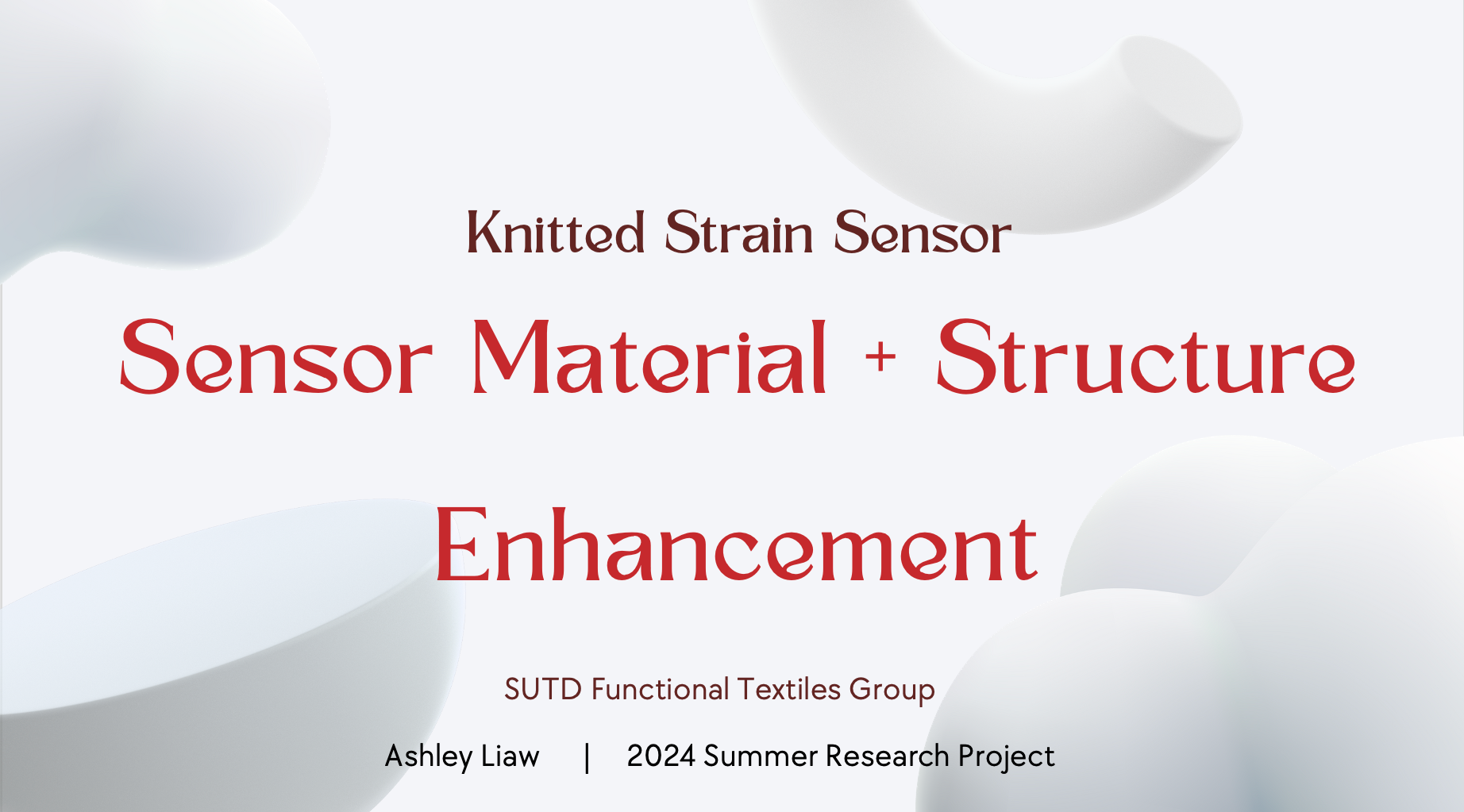
Enhancing Monocopter Directional Movement Through Mid-Flight Wing Shape Manipulation
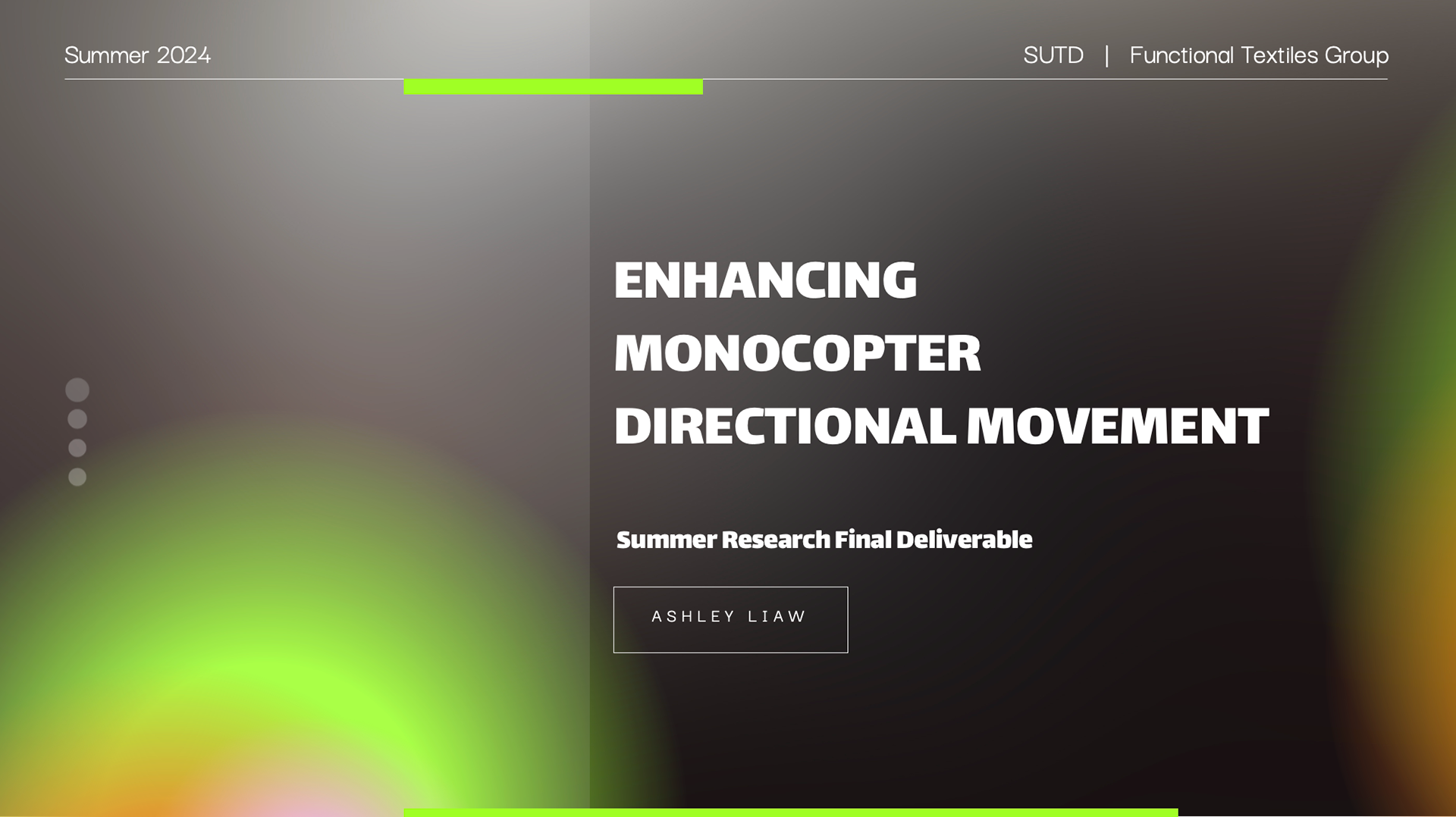
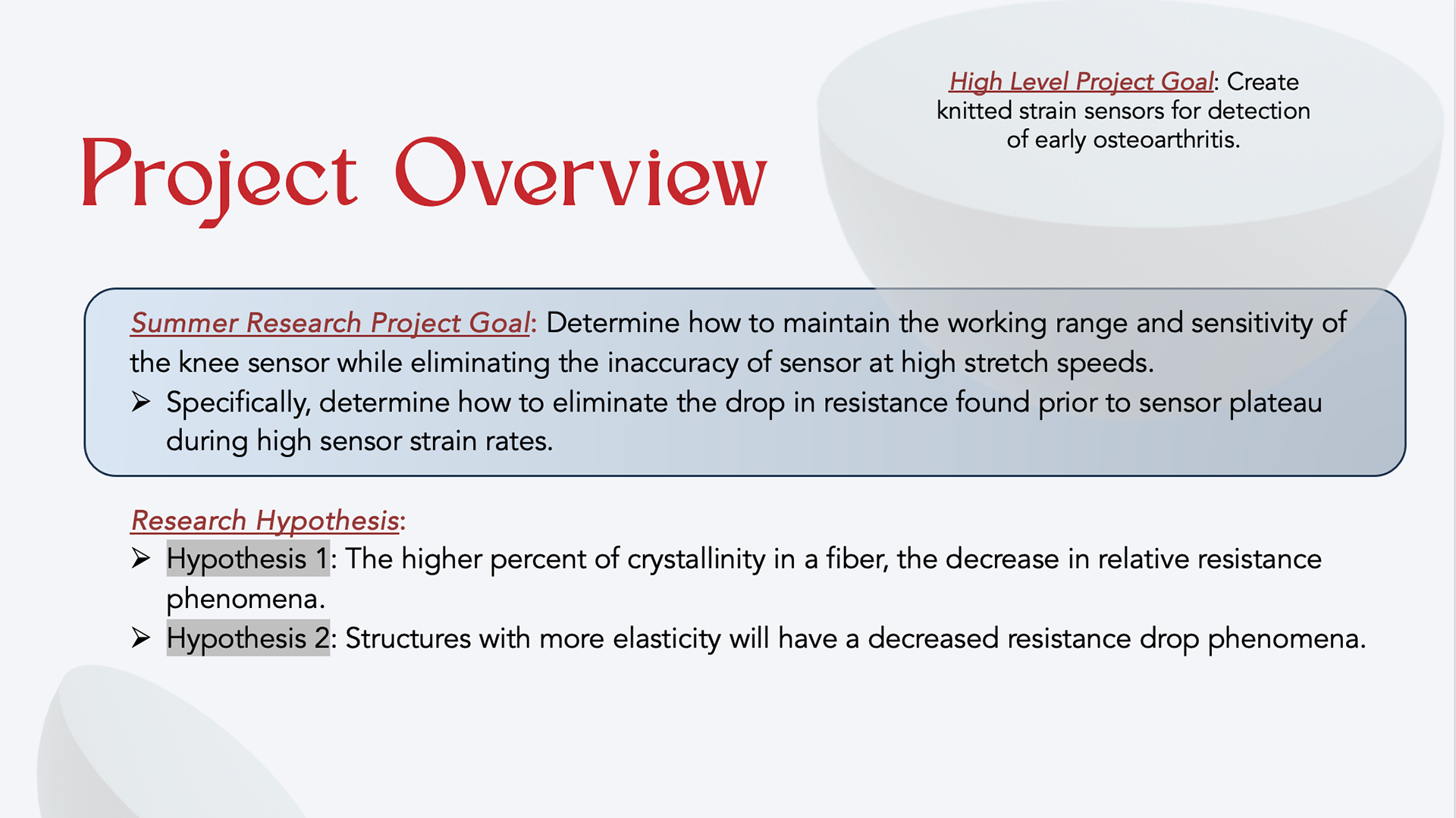
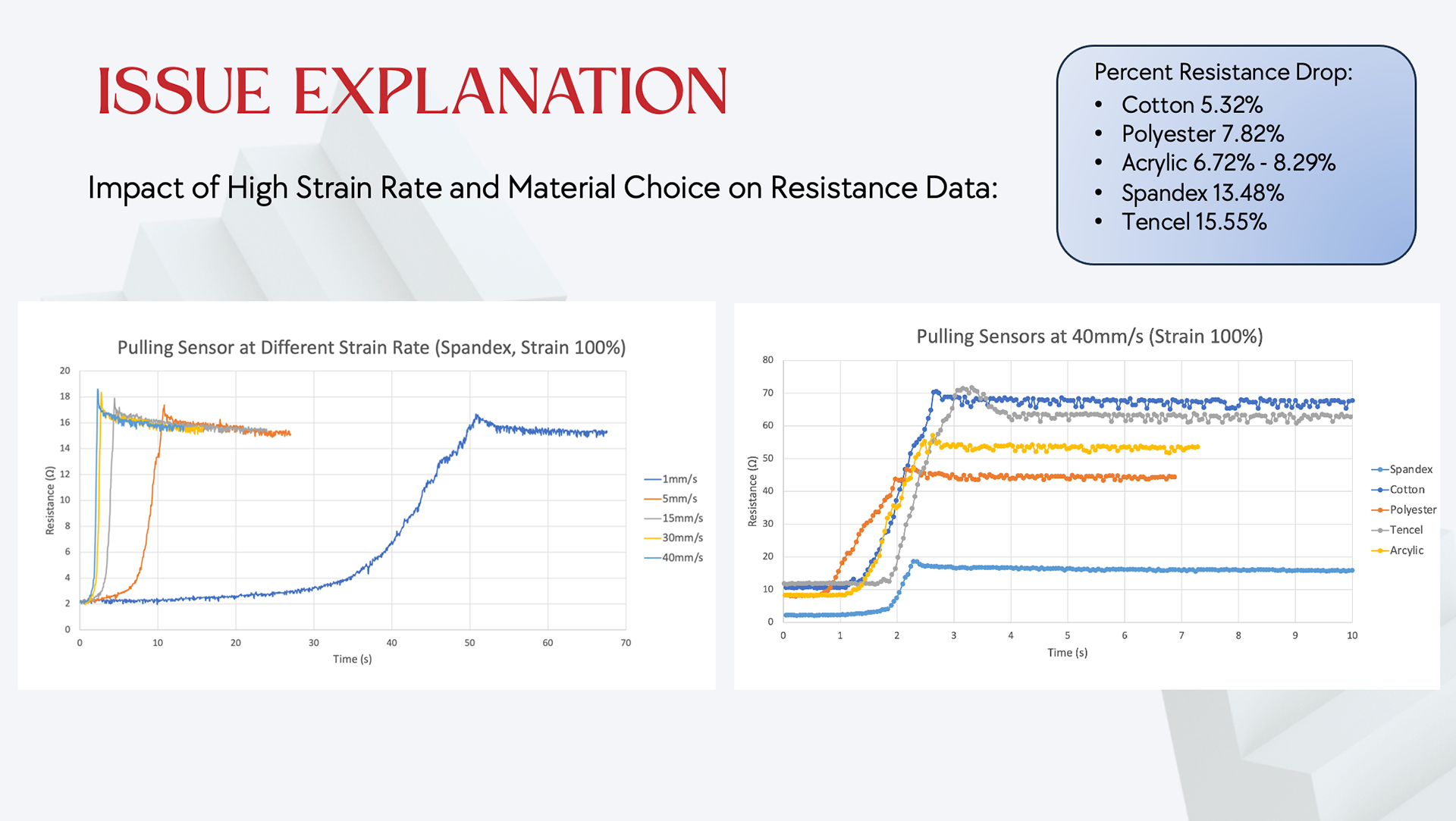
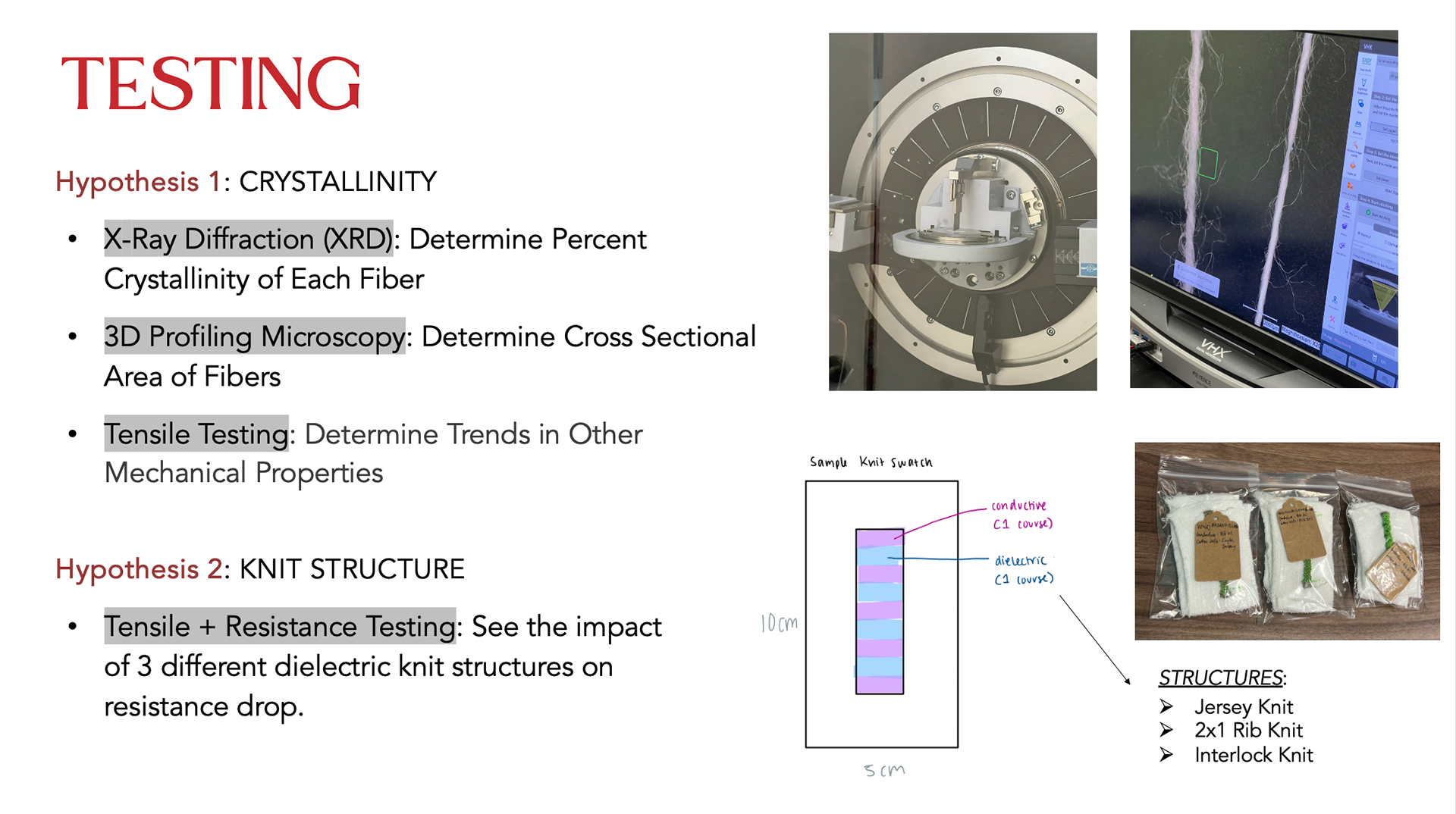
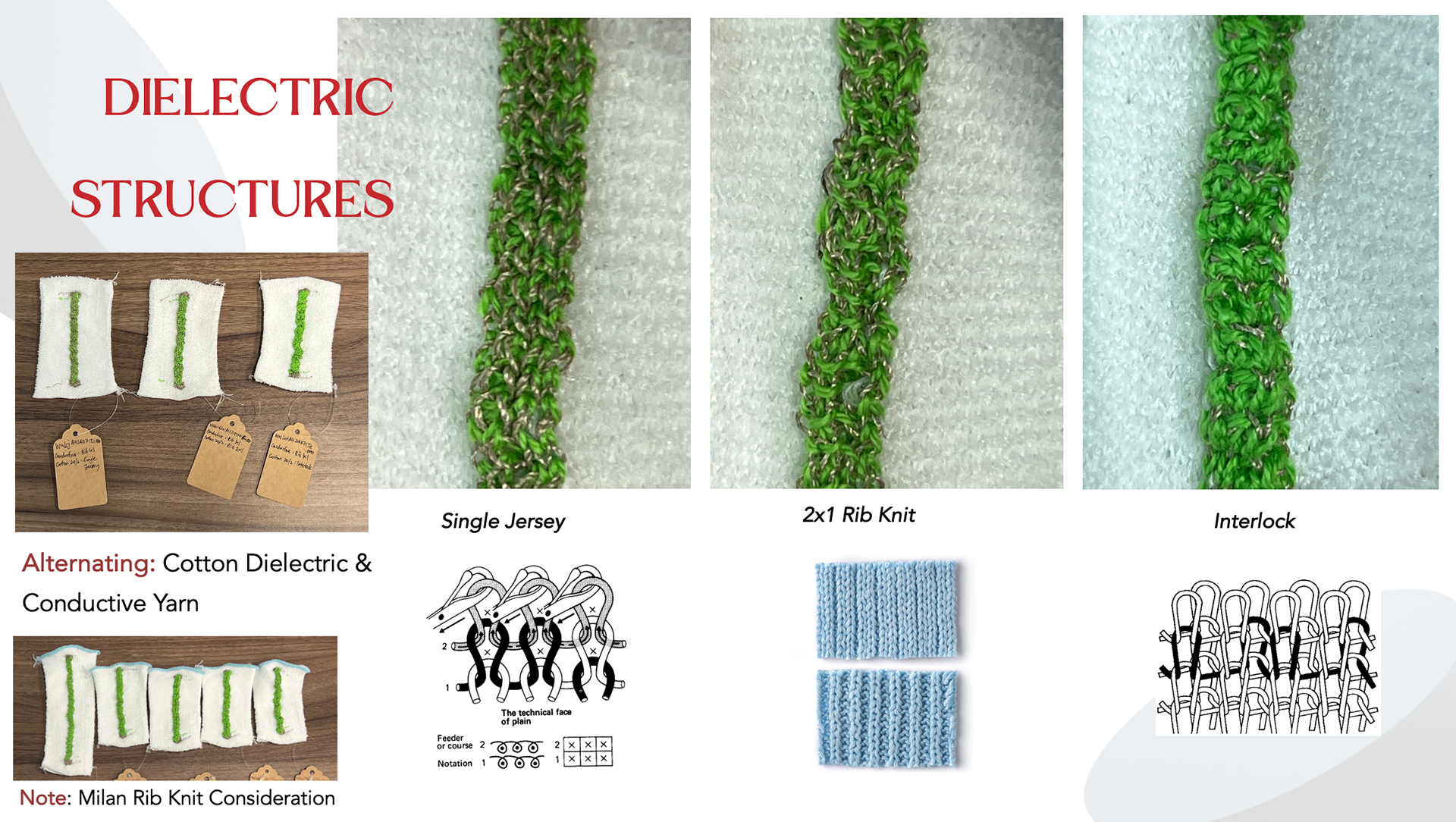

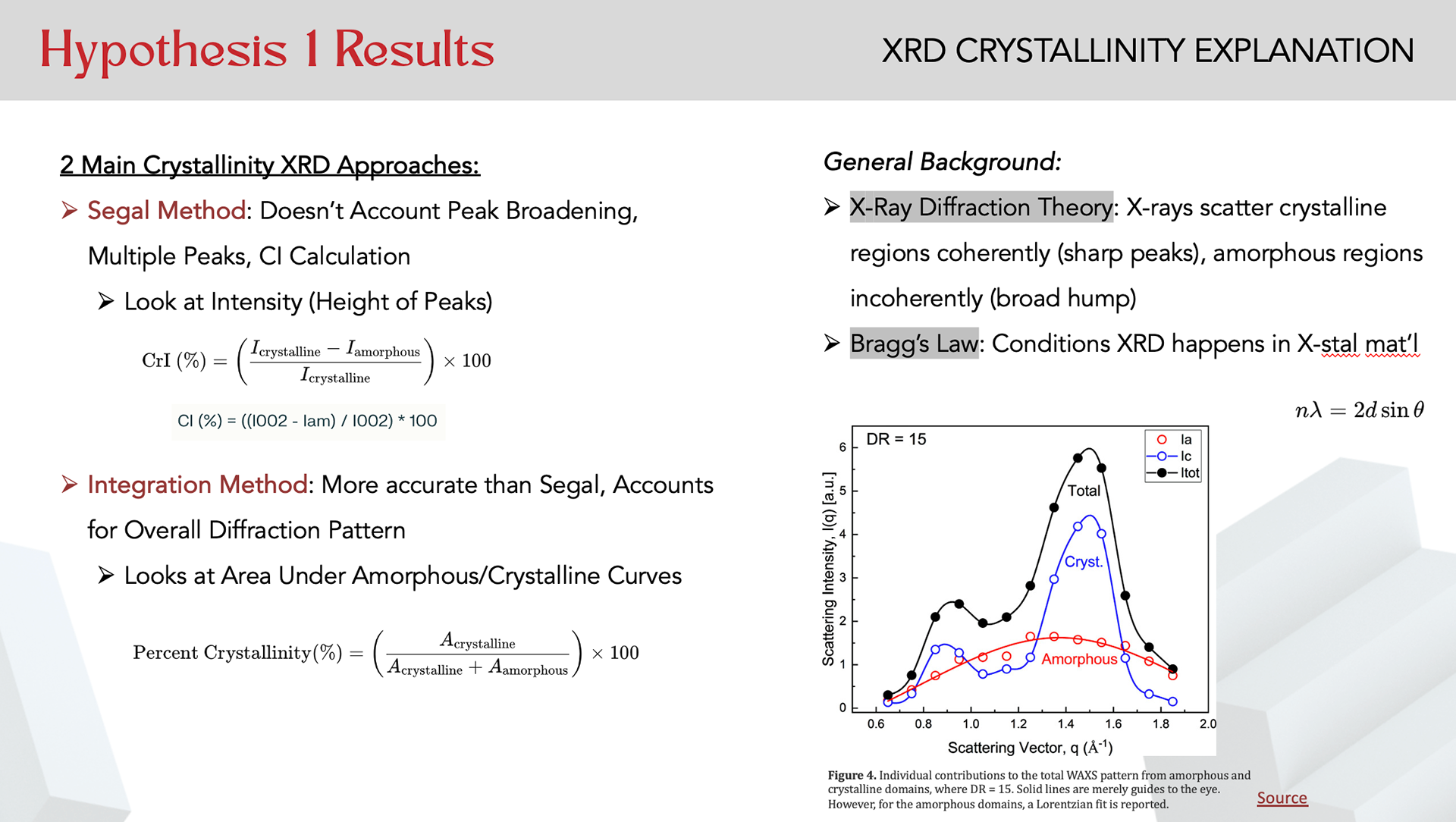
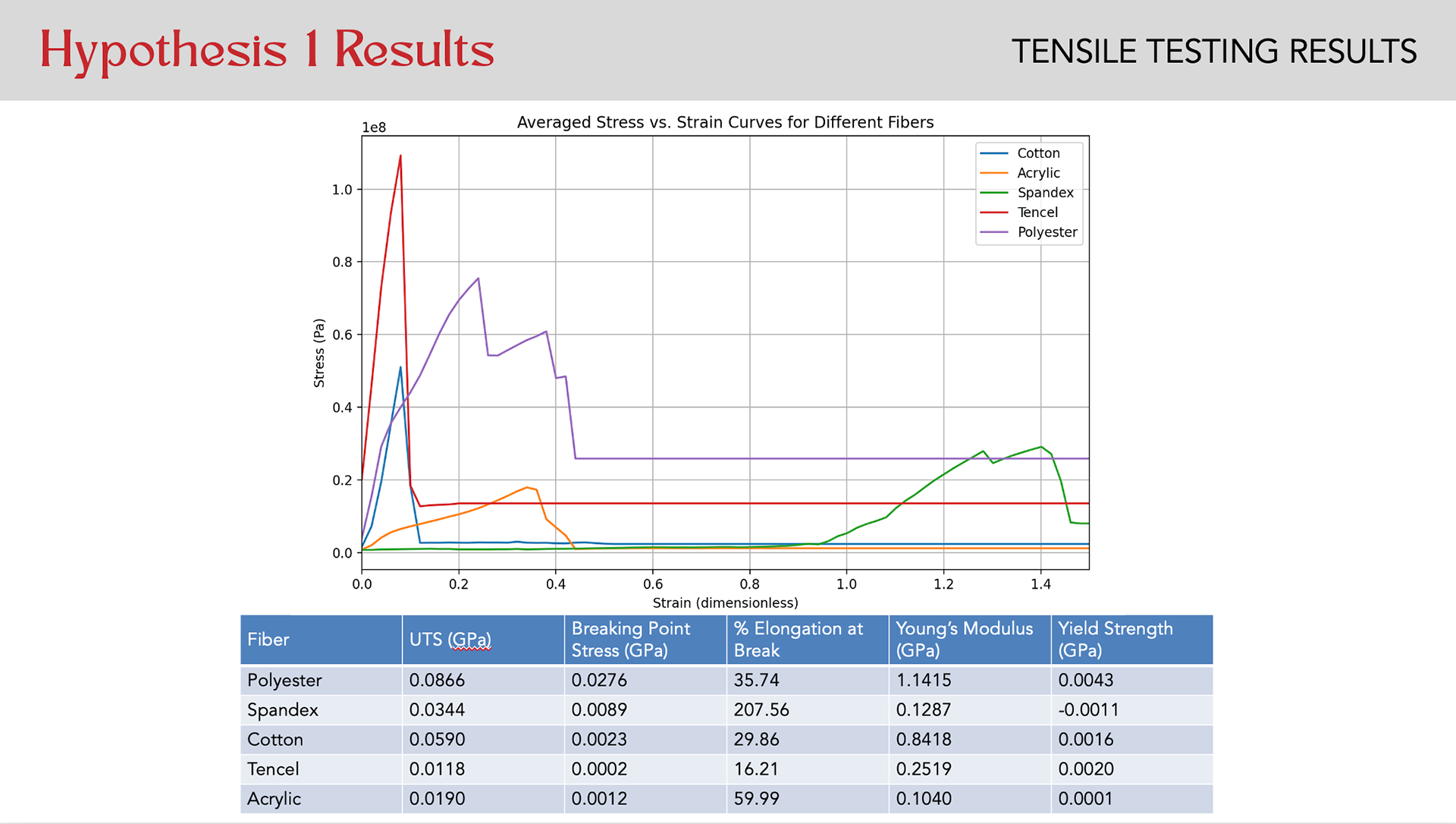
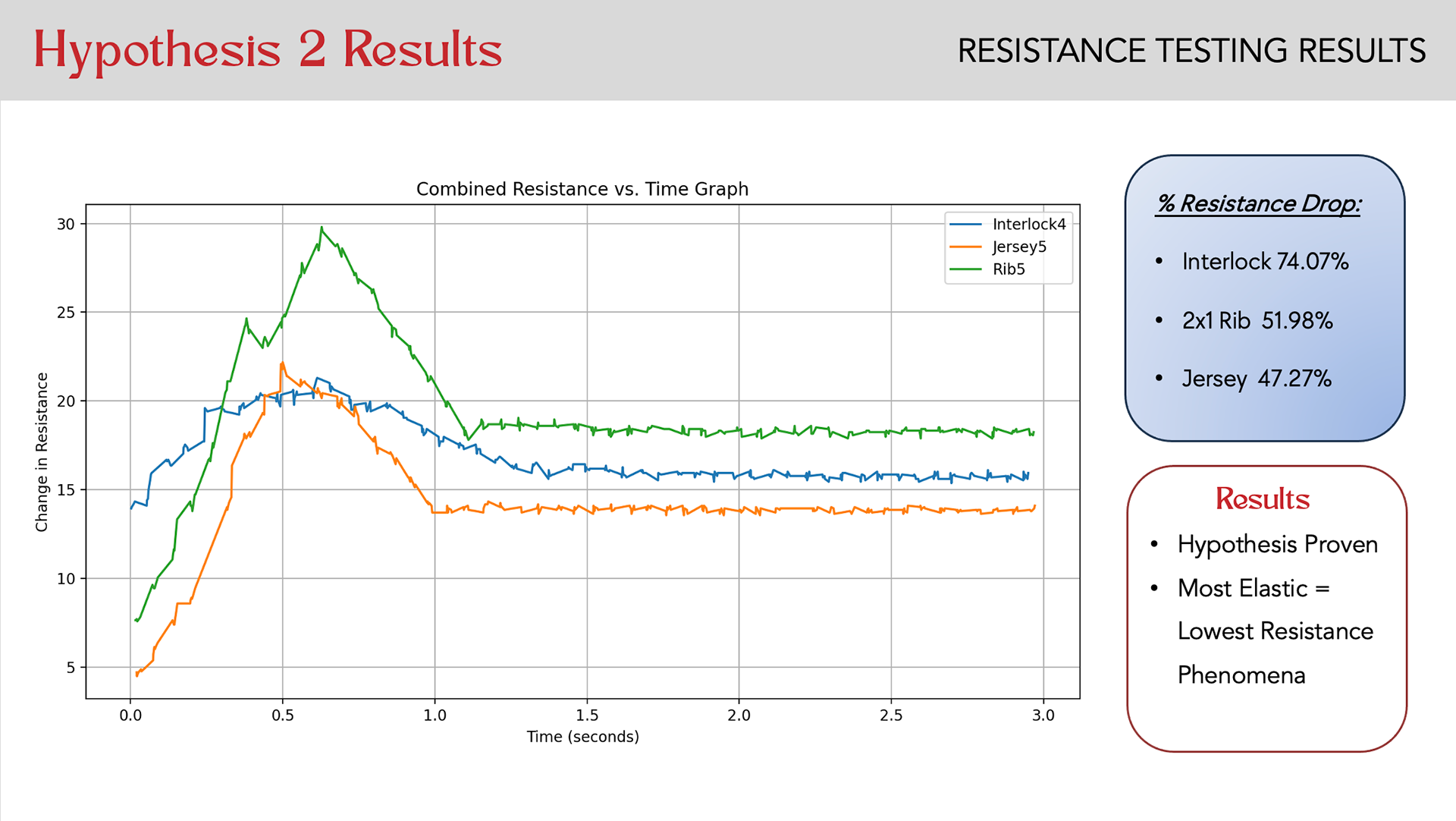
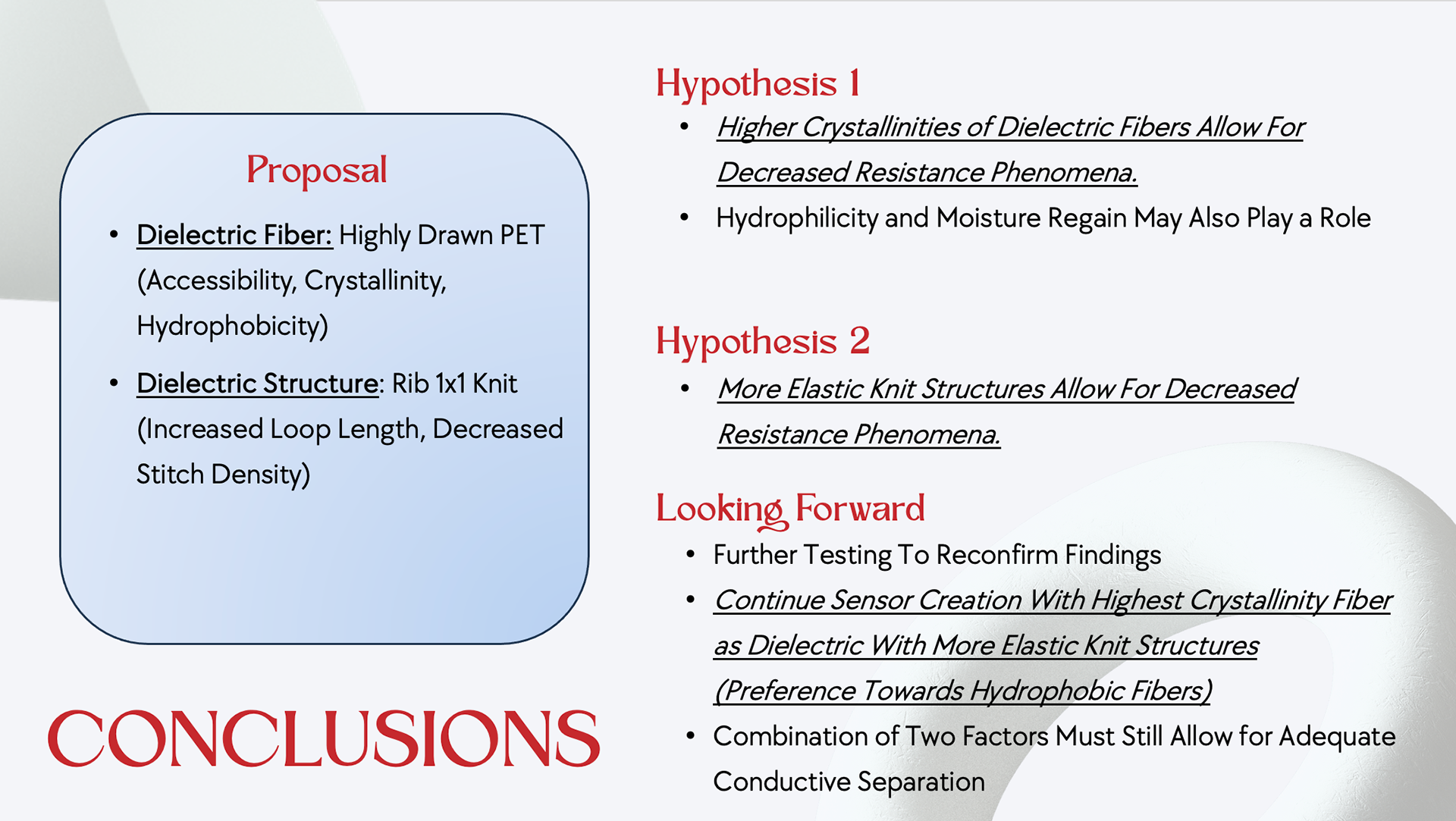
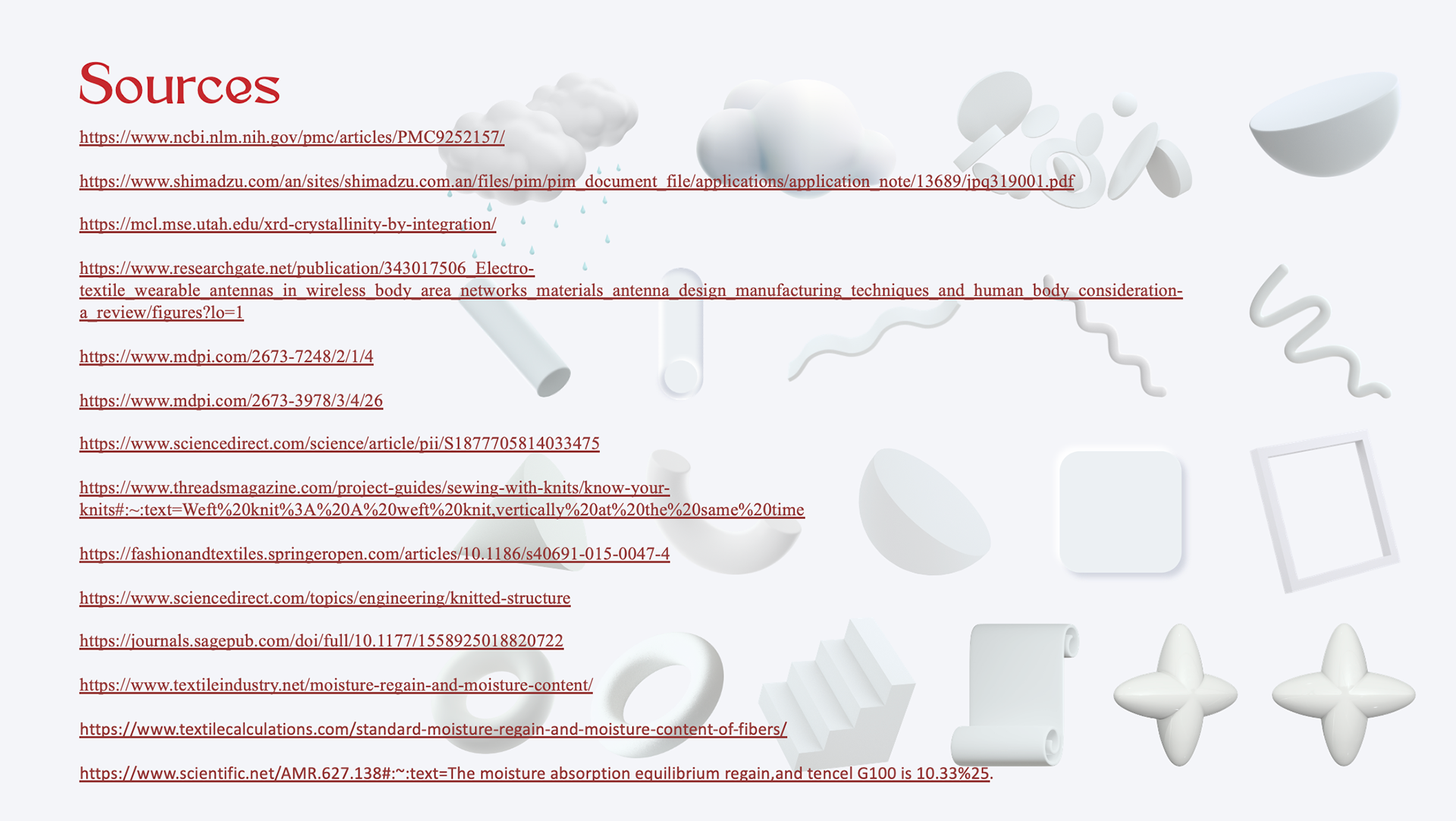
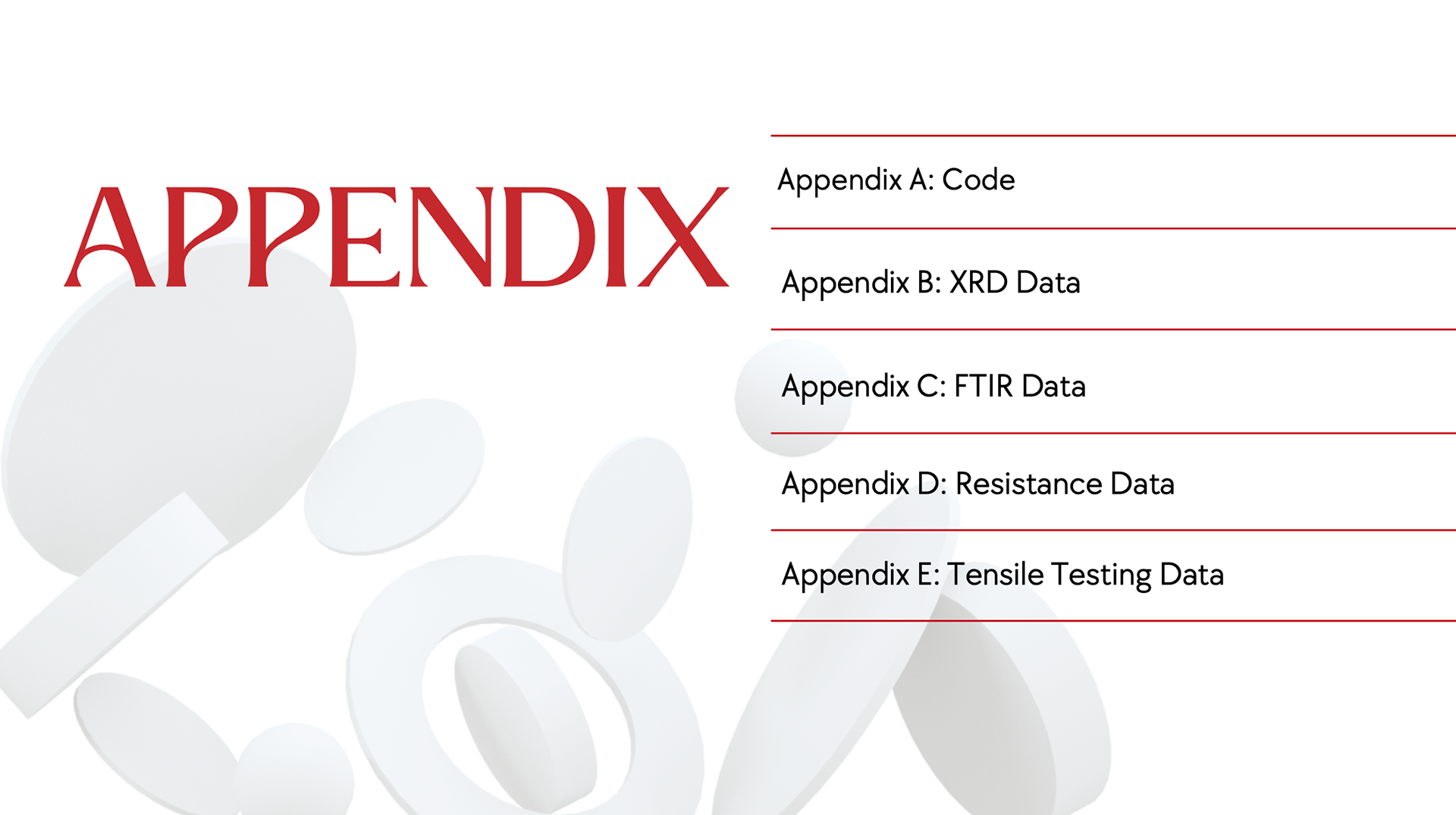
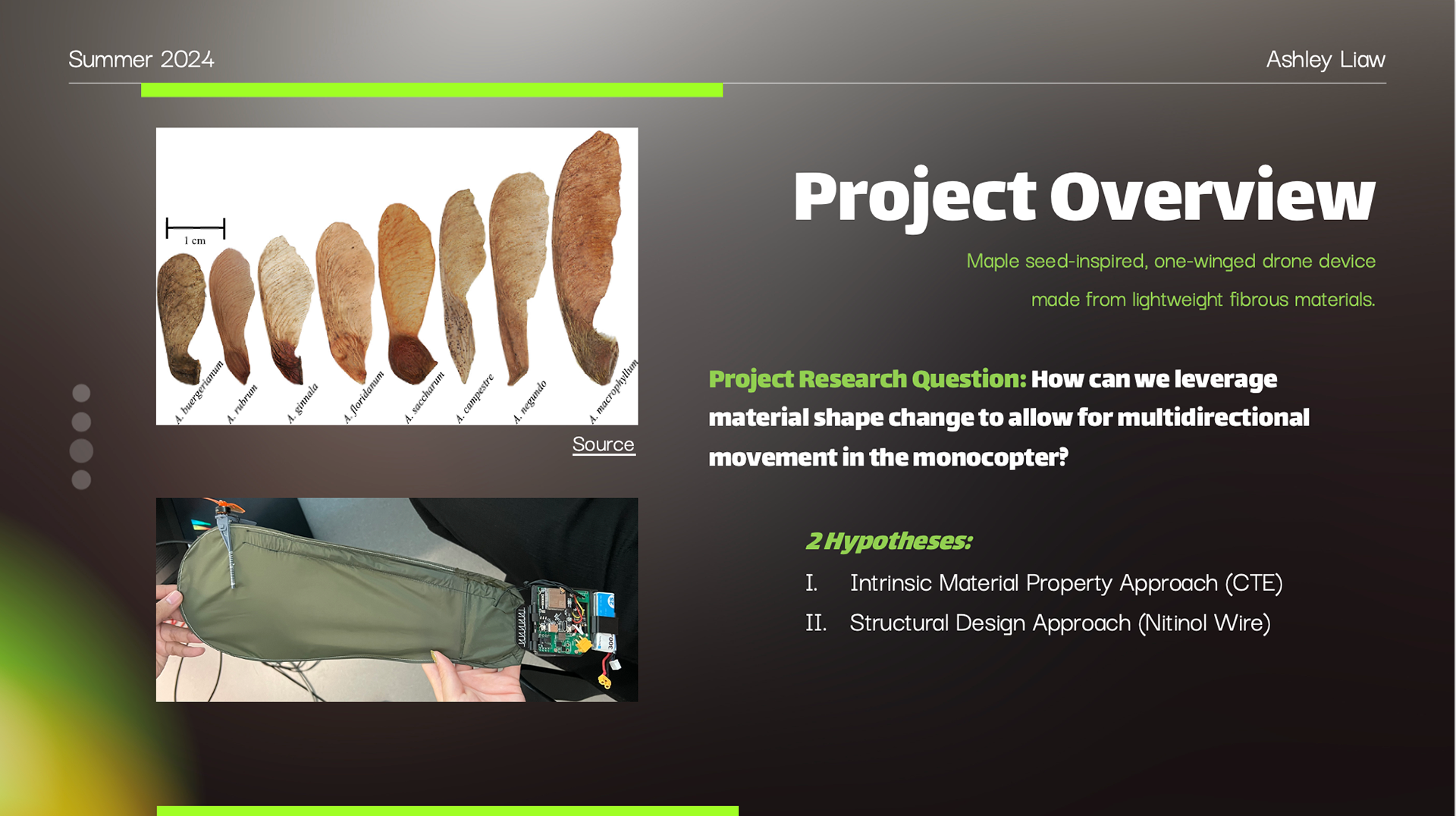
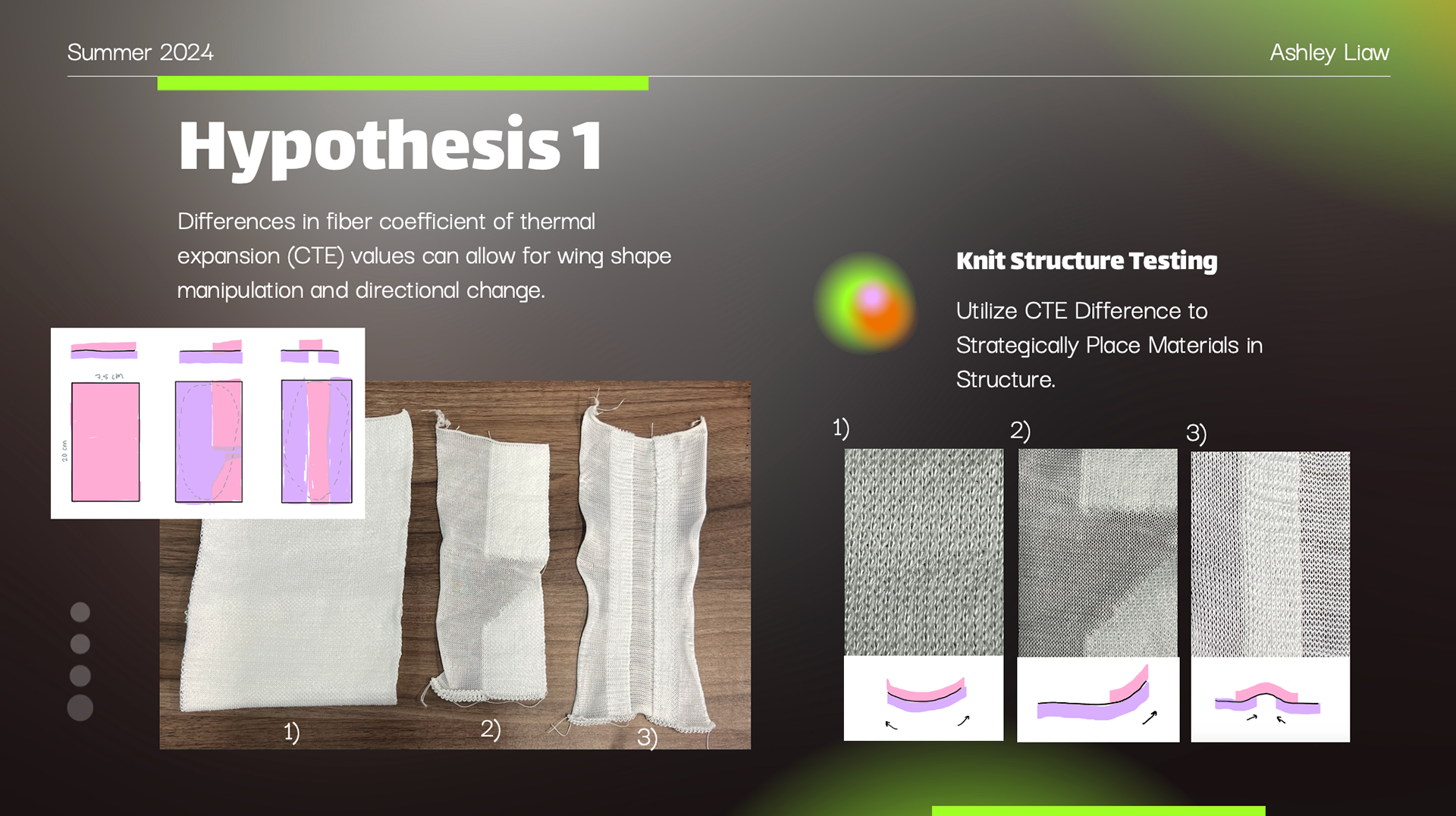
Due to limited time and resources, I utilized the CTE difference of PET and UHMWPE as a base to examine material behavior in the three different knit structures above. These learnings would inform more strategic material choices and knit structures later.
Hypothesis 1 Data + Results
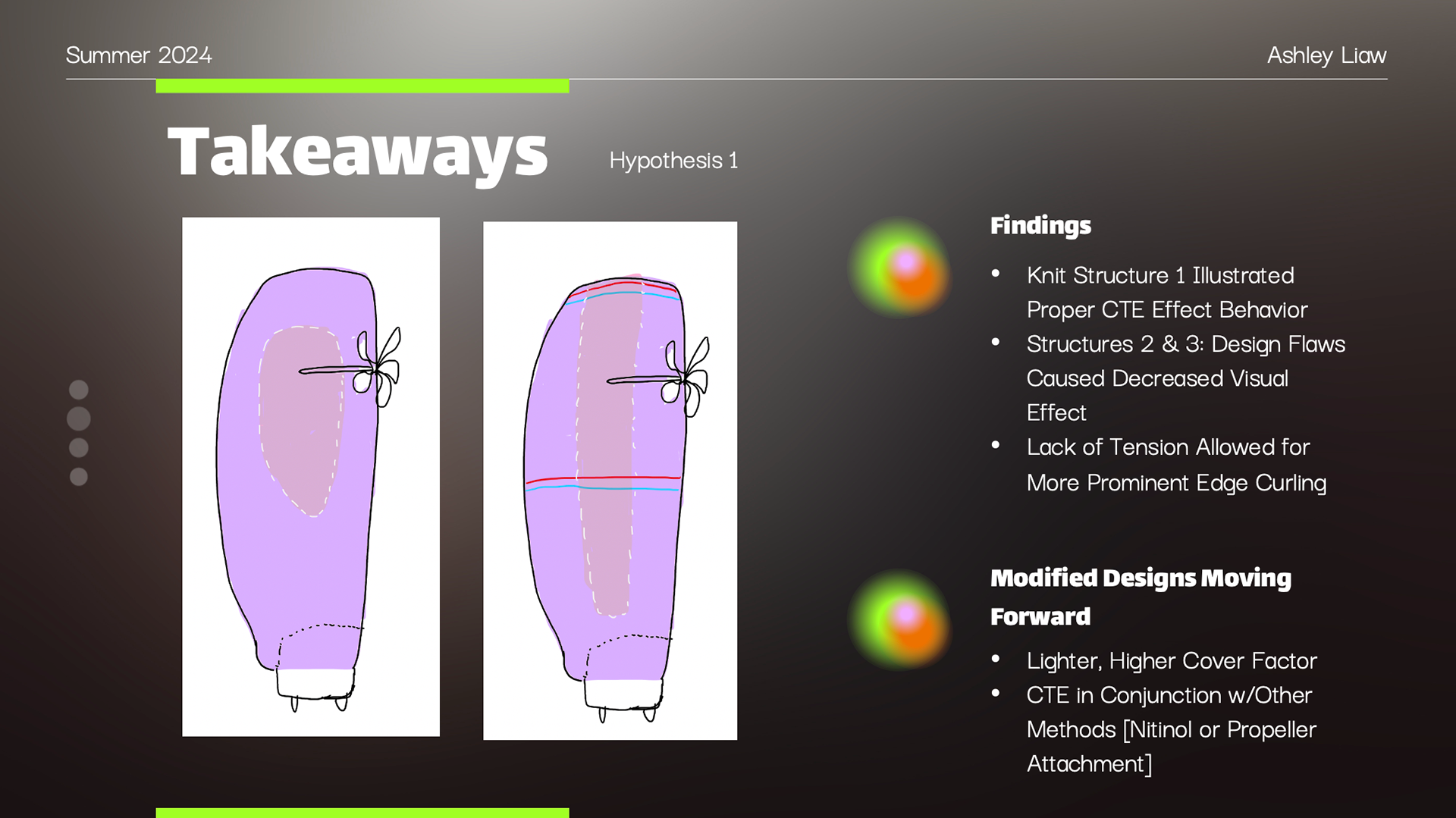
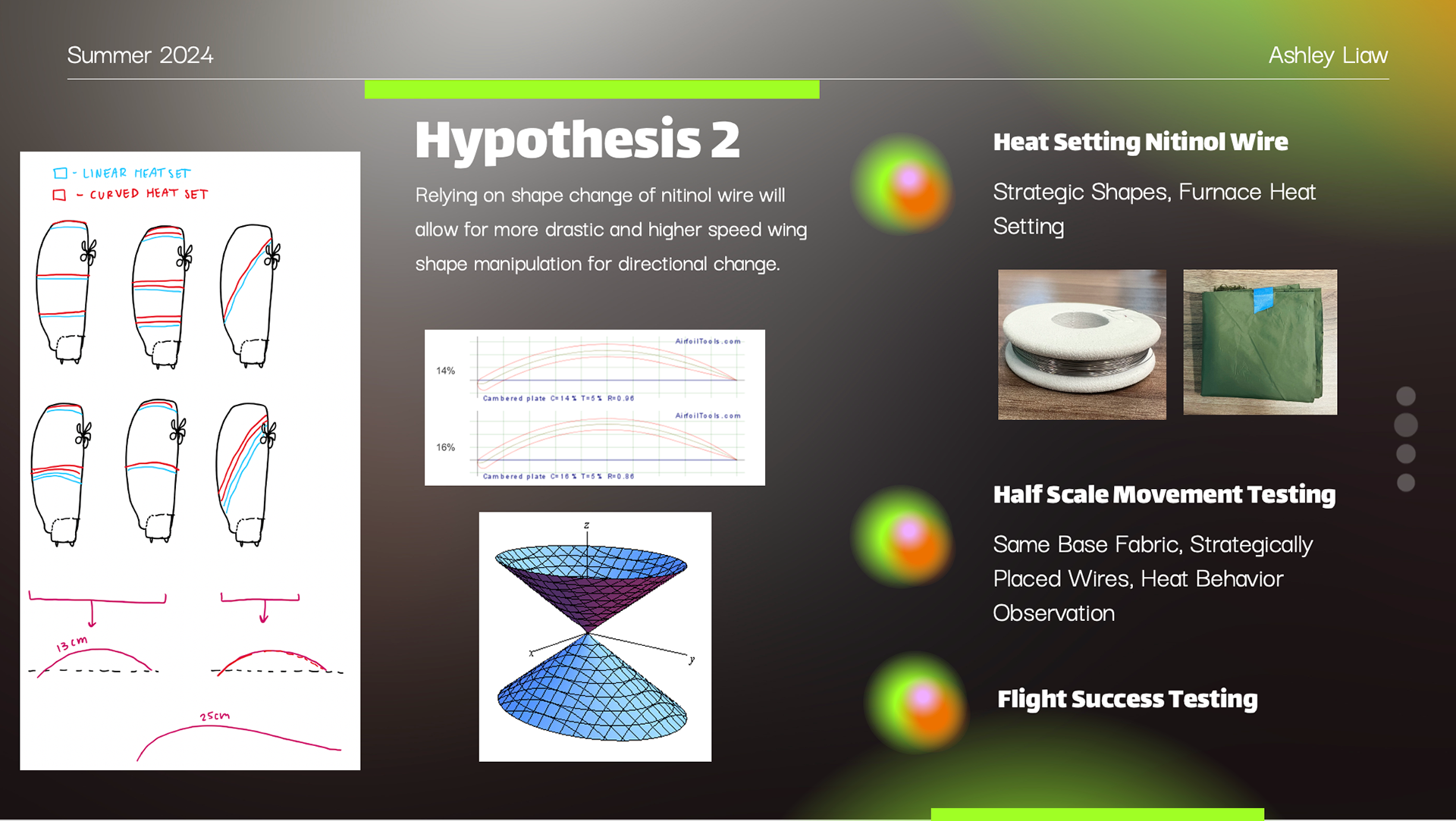
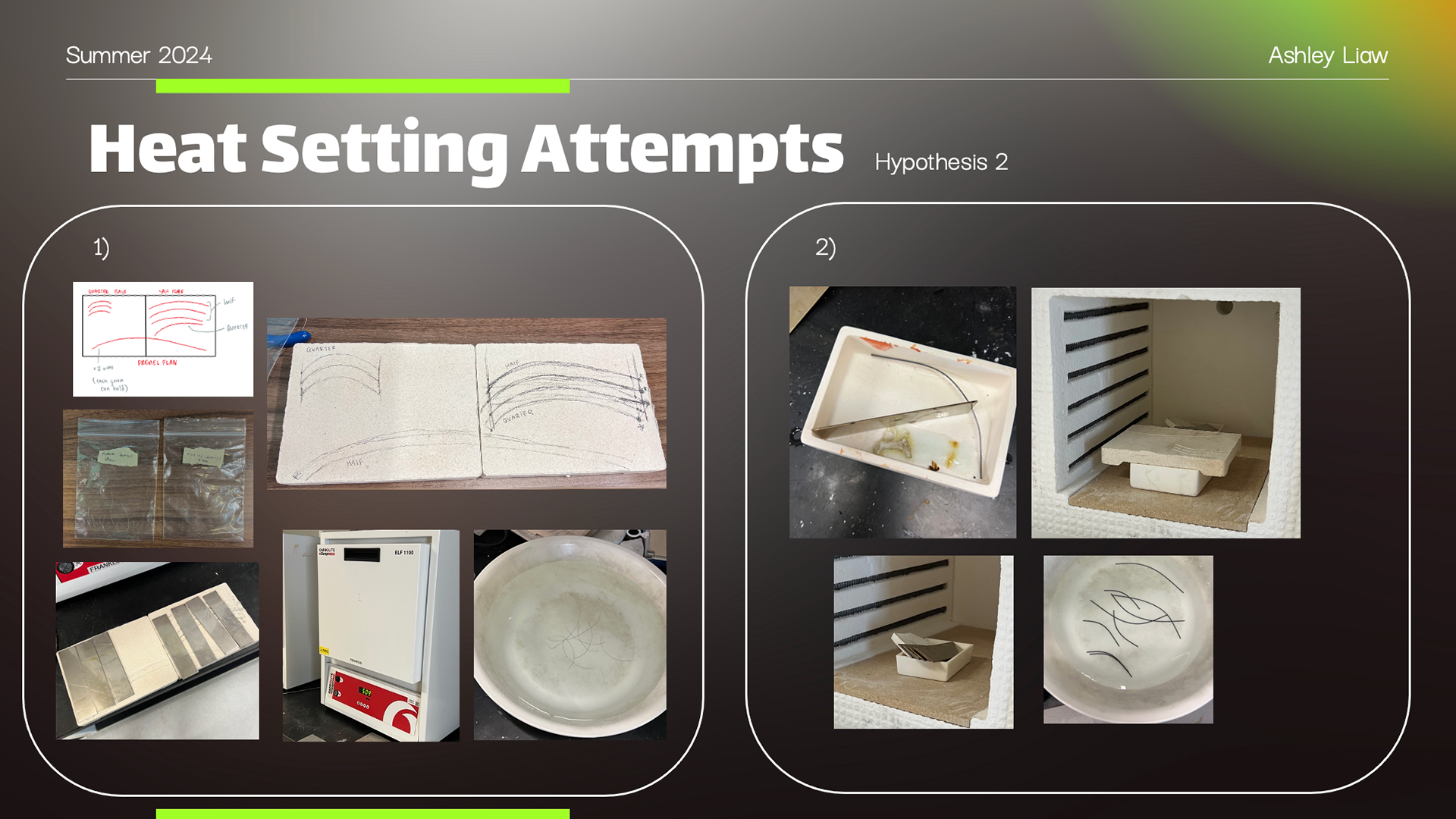
I encountered challenges in sourcing the right nitinol wire and determining the most effective method to heat-set specific shapes. Initially, I attempted to dremel refractory bricks into my desired airfoil-inspired form, but the mold could not withstand the wire's strong force. As a result, I had to innovate and repurpose existing lab tools, as seen in section 2, to achieve the desired shape.
After successfully heat setting my nitinol wire, I tested the wire's ability to return to its heat set shape once exposed to a heat stimulus (in this case, warm water).
Half Scale Monocopter Wing Shape Change Testing
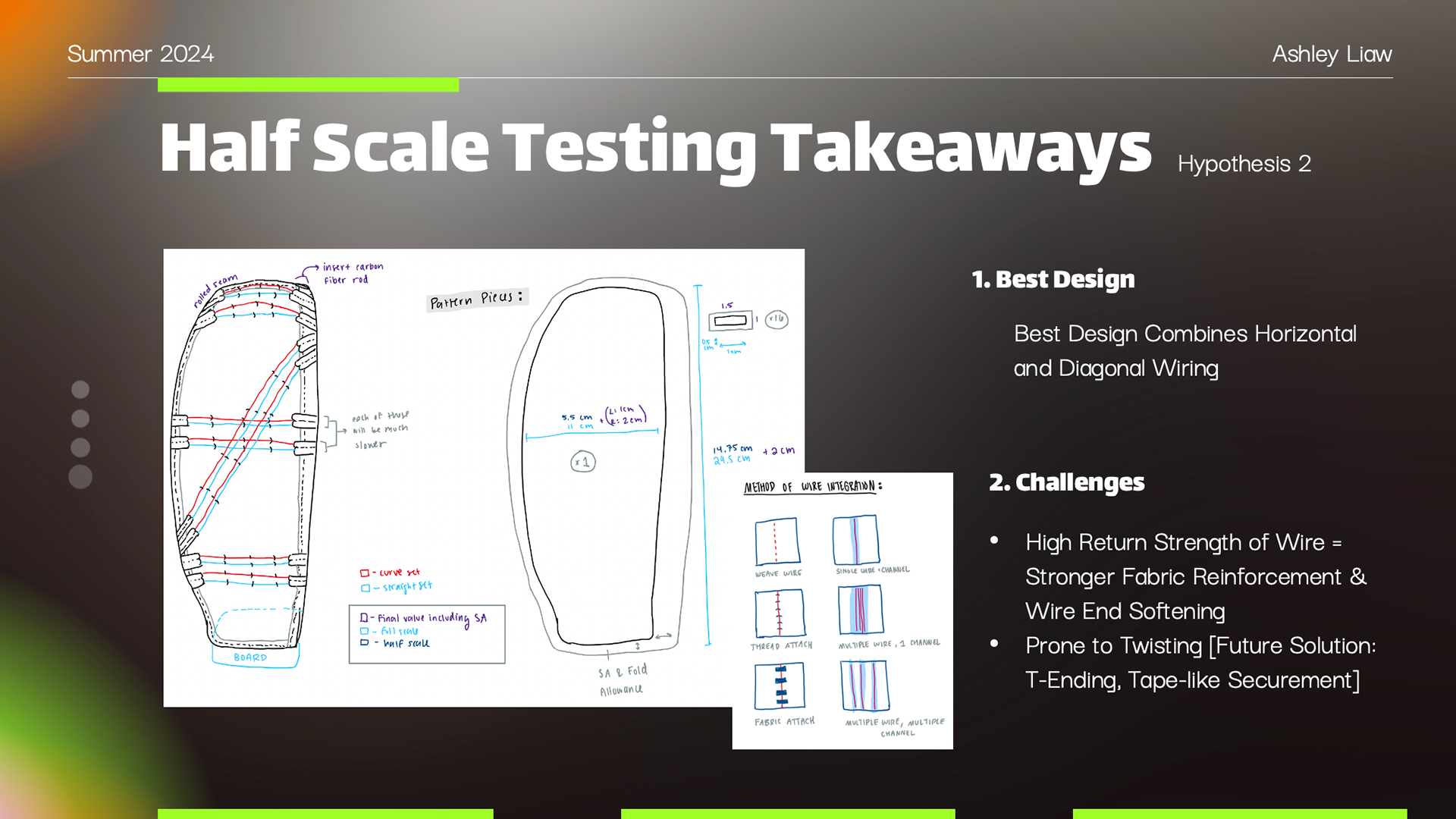
Full Scale Wing Testing with Finalized Wire Placement
Analysis of Monocopter Flight in Unactivated and Activated Wire Wing Shapes
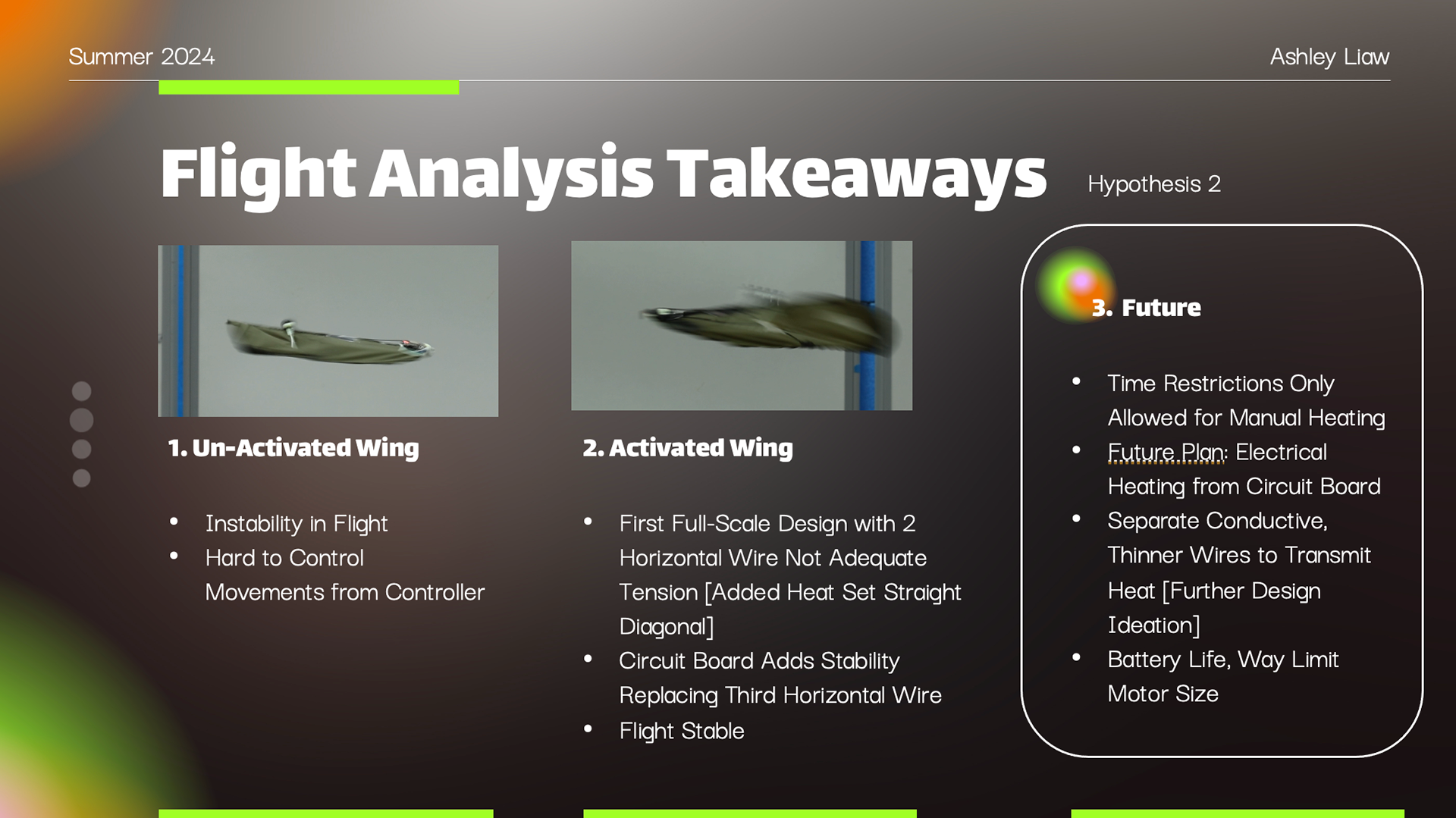
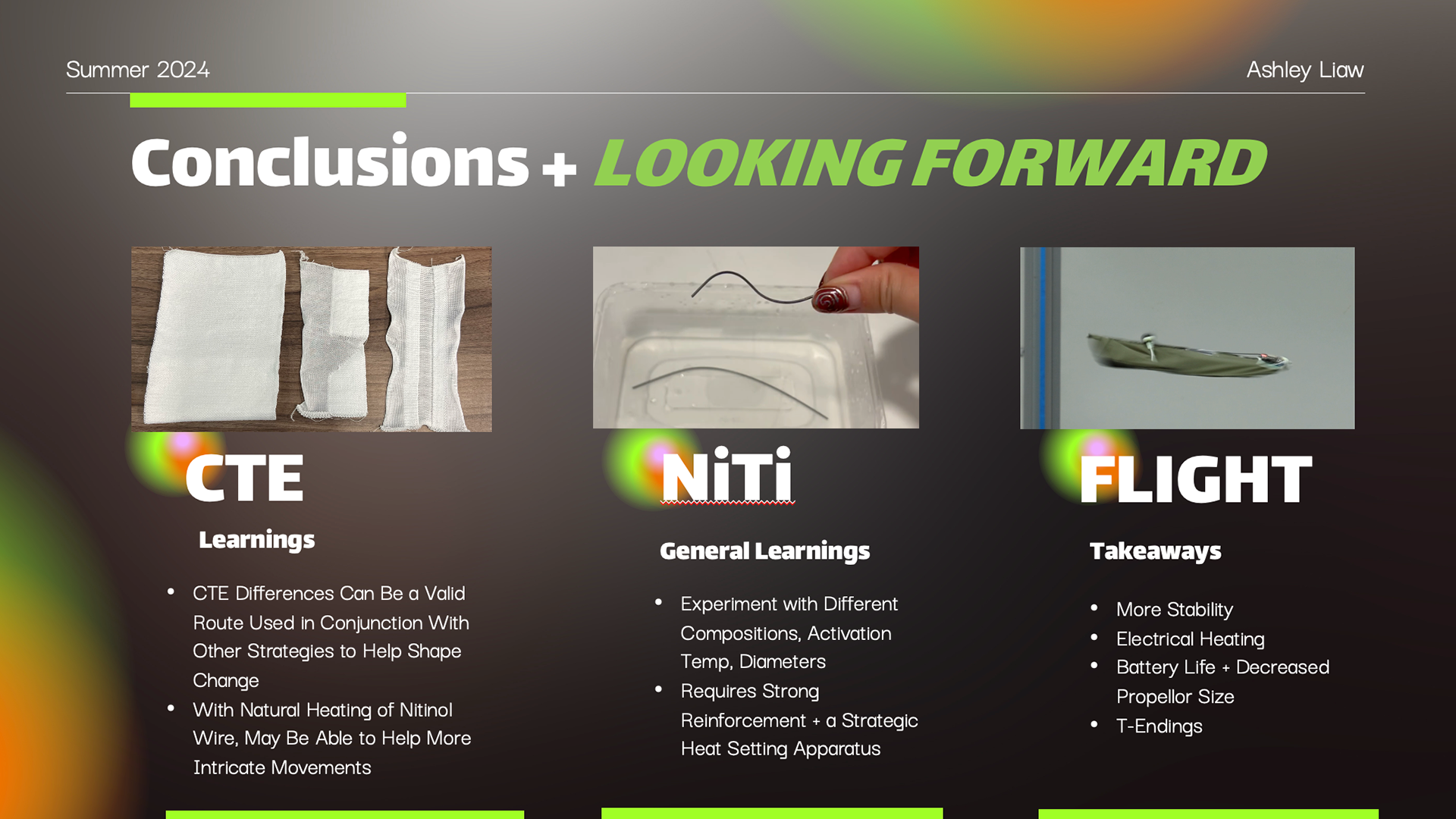